Cascading Fan Application at Welding School, Portland Community College
- David
- Aug 25, 2021
- 2 min read
Updated: Apr 16
The Ultimate & Most Energy-Efficient System
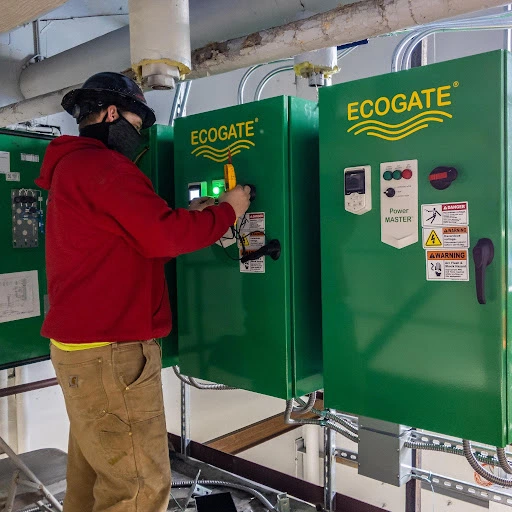
When preparing for the new welding shop at Rock Creek Campus of Portland Community College in Oregon, College officials sought a project specification that called for the most energy-efficient system available for exhaust ventilation. The ideal system would work with maximum efficiency, whether only one or all 75 welding booths were in operation.
Cascading Fans System
The best option for designing a system with such a wide range of air volumes is a "cascading fans system." Commonly used in Europe, an example can be seen in our case study from Crystal Doors in the UK.

How the system works: When only one welding booth is in use, only the first fan starts. As more welding booths are used, the fan increases air volume by running at higher RPMs. If the air volume of a single fan is insufficient, a second fan starts, and so on.
Why it's better compared to one larger fan: A single fan running at higher speeds generates enough pressure to overcome all system losses (by hoods and duct systems) at lower air volumes.
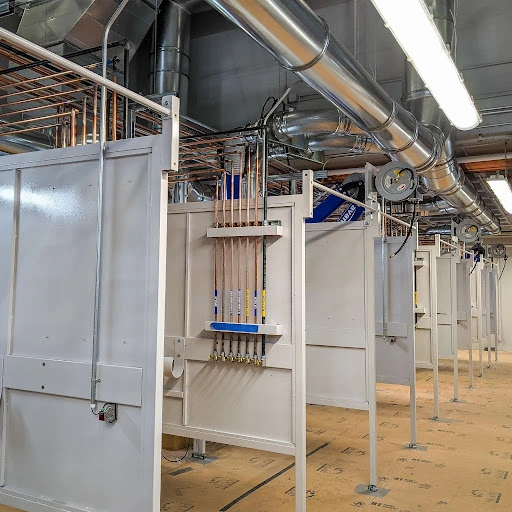
The cascading fans system uses Ecogate's “Optimized Cascading Fans mode” and the Closed Loop mode, where fans are regulated to provide the exact requested air volume. If one or several fans/motors/VFDs fail, the greenBOX software automatically replaces them with the next available fan/motor/VFD, ensuring the system continues to operate.
Achieved Electricity Savings Compared to Conventional Ventilation System
The on-demand ventilation system achieves excellent results compared to conventional systems: when only one booth is in operation, savings are 96% of electricity; with ten booths, 85%; with 20 booths, 72%; and with 30 booths, 61%. Additional savings are achieved by the reduction of make-up air, based proportionally on the number of booths in operation.

Honeywell Tridium Building Automation System
The greenBOX Master control system is connected to the Honeywell Tridium Building Automation System, which reads data from the Ecogate system for monitoring, energy use evaluation, and measured air volume of the ventilation system. The measured air volume is used to adjust the make-up air system.
Summary

This article describes a highly energy-efficient ventilation system for welding booths installed at the welding shop of Portland Community College Rock Creek Campus in Portland, Oregon. Additional benefits include make-up air savings, automatic system start & stop, and reduced noise in the shop.
Project design: Opsis Architecture, LLP
Project management: Pence Construction, LLC
Welding exhaust system: Avani Environmental Intl. Inc.
Comments