

Ecocate's Control System
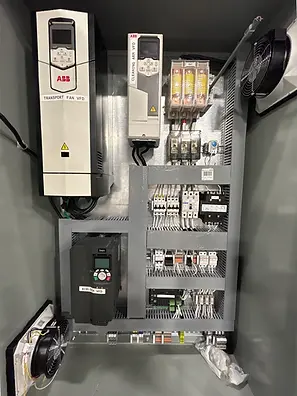
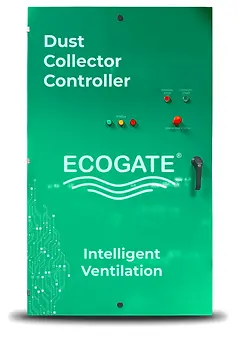
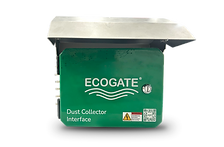
Ecogate’s Dust Collector Controller gives each collector its own intelligent control hub, monitoring fan performance, filter health, airflow, and environmental conditions in real time. With built-in inputs, outputs, and seamless greenBOX integration, it automates start/stop, protects equipment, and delivers complete visibility across your dust collection system.
Dust Collector Controller
Installation Material

Ecogate Master Cable
Ecogate Master Cable connects Smart Gates and the Power Master VFD to the greenBOX controller. It's also compatible with the greenBOX 12 for connecting the Power Master VFD. The gates and VFDs are connected in a daisy-chain, this simplifies installation as it reduces the number of cables necessary for installation.

Flange-to-QF Adapters
For those utilizing QF (Quick-Fit) duct systems, our QF adapters feature an industry-standard angle flange on one end and a Quick-Fit rolled edge on the other, allowing you to easily install one of our gates to your QF duct system.
Add-Ons
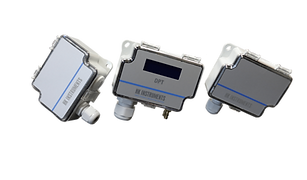
Winter Mode Sensor Kit
Enhance your Ecogate On-Demand Control System with our Automatic Winter Mode feature. This kit includes two temperature sensors—one for measuring ambient air near the dust collector filters and another inside the ducting. As temperatures near freezing, the fan automatically operates at a slower pace to prevent filter bags from freezing, eliminating the need for manual start-stop operations. This smart feature allows the fan to run at a low, adjustable speed, achieving up to 85% electricity savings during winter mode compared to full-speed operation.

Netbook for greenBOX 12 System
Designed for smaller shops with up to 12 workstations, the greenBOX 12 controller offers a cost-effective solution. Our Netbook for greenBOX 12, equipped with pre-installed Ecogate software, simplifies both the setup and monitoring of your system. Plus, its remote access capability allows us to provide you with prompt support and assistance, ensuring smooth operation and peace of mind.