
Smart Automation for
Dust Collection


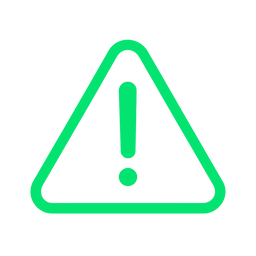
💡 Conventional industrial ventilation works the same way—one switch for the entire system, wasting electricity and money.
âš¡ Ecogate gives every workstation its own automatic switch, delivering airflow only where and when it’s needed.
​
DON'T open ventilation to machines not generating dust!
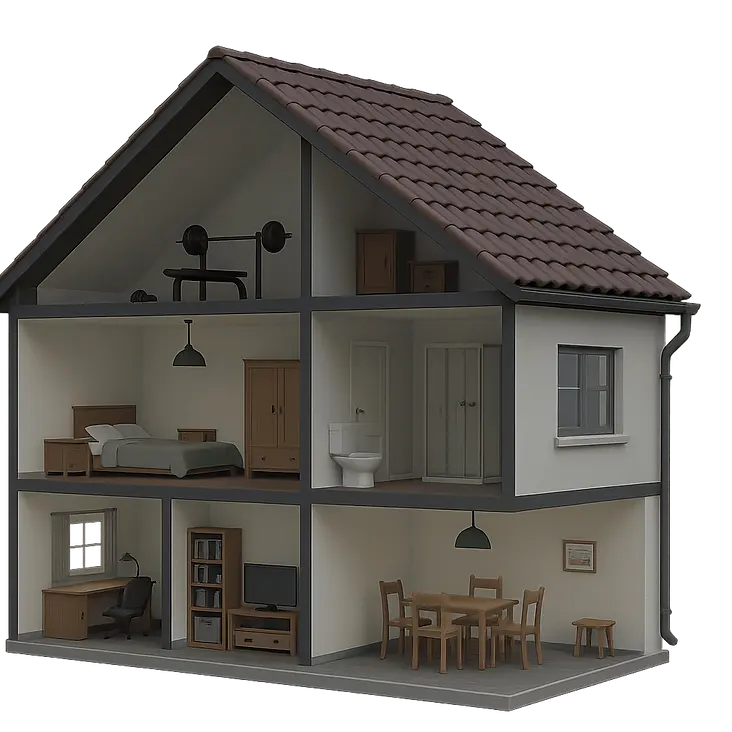
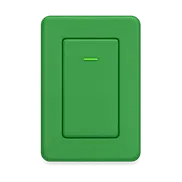
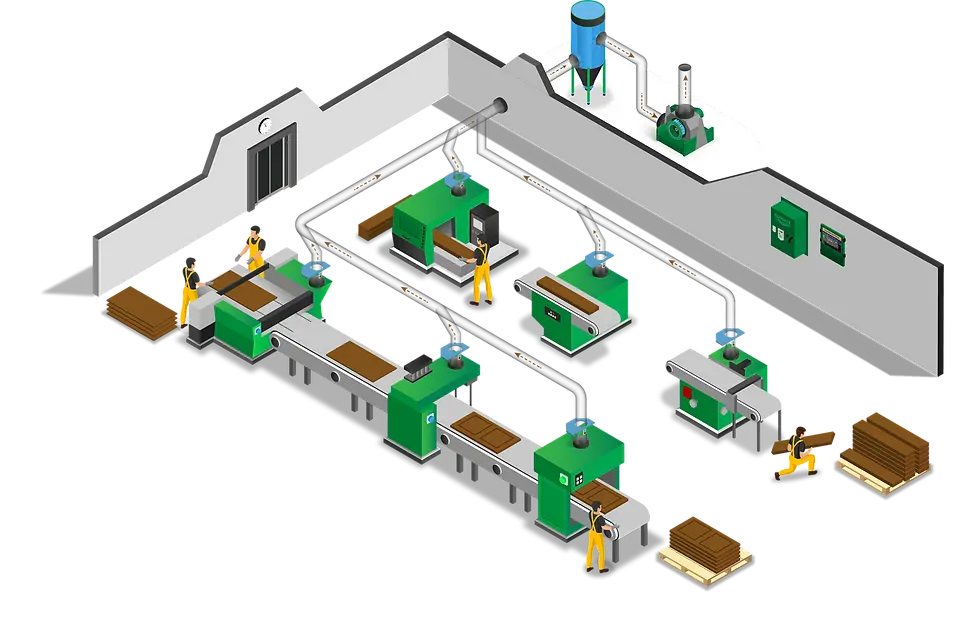
1
2
3
4
5
Power Master VFD adjusts fan speed based on real-time demand, reducing energy.
The greenBOX calculates the exact airflow needed and opens or closes gates in real time.
Any dust collector error automatically stops the fan.
Triggered by the sensor, the Smart Gate opens for active machines, directing airflow only where needed.
Sensors detect when a machine is about to generate dust or fumes.
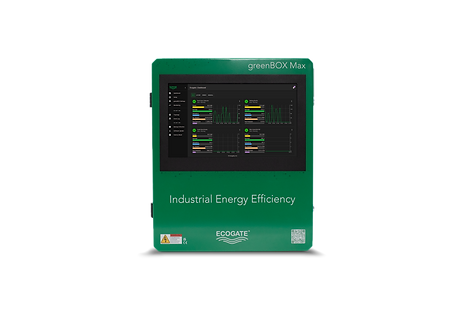


greenBOX Control Units 72, 144 & 288 gates

Power Master VFD
230 V, 460 V & 575 V
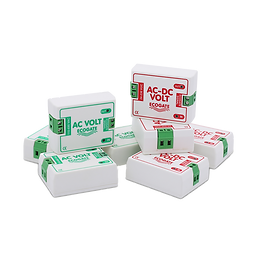
Workstations
Activity Sensors

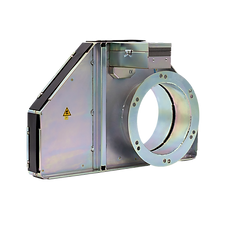
Smart Gates
2" to 26"

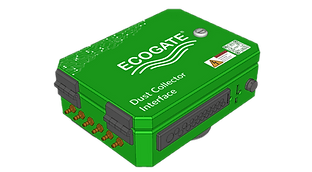
Dust Collector Controller
Dust Collector Interface


Airlock
2HP
Cleaning Arm
2HP
Cleaning Pump
20HP
Transport Fan
20HP



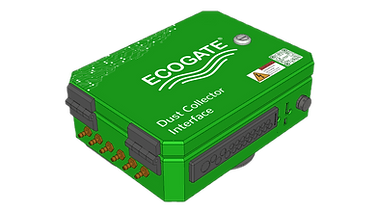
-
Averaging Air Velocity/Air Volume Sensor
-
Filter differential pressure
-
Fan total static pressure
-
Ambient air temperature, and humidity for Winter Mode
-
Dust level (calibrated PM1, PM2.5, PM10 level)
-
Air quality (TVOC, eCO2)
VFD Stall, Underload, Overload Protection meaning no Zero Speed sensors needed
Gentle starts cut mechanical shock extending motor life
Superior to contractors
6 in 1 Sensor Suite
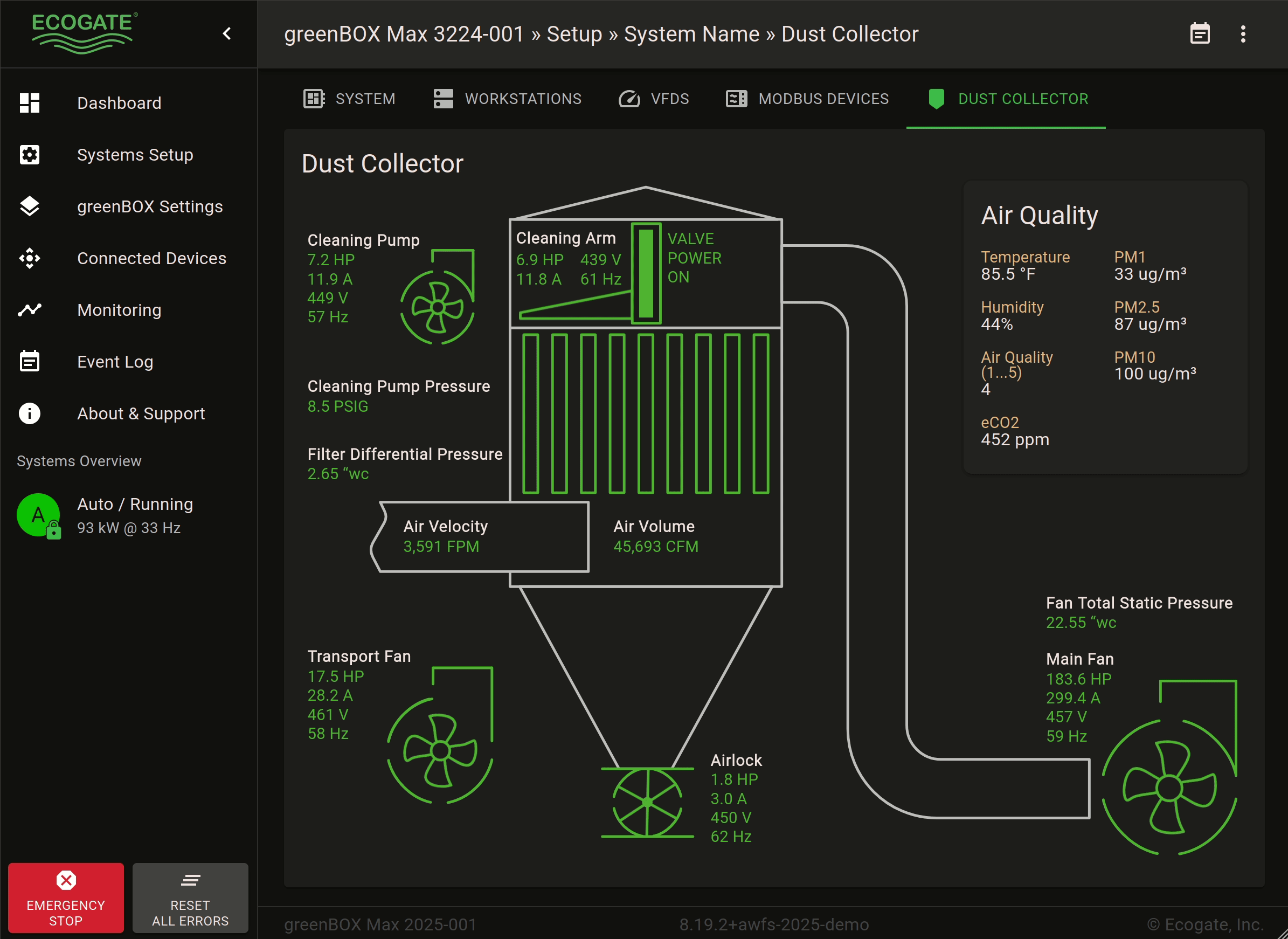
Detailed monitoring of RPM, current voltage and power
​
Modern, web-based user interface with built-in remote access
​
Easy, user-programmable logic and automatic updates over costly on-site tech visits
​
Compatible with any dust collector brand
​
No other competitor can fully automate dust collector start/stop based on workstation activity


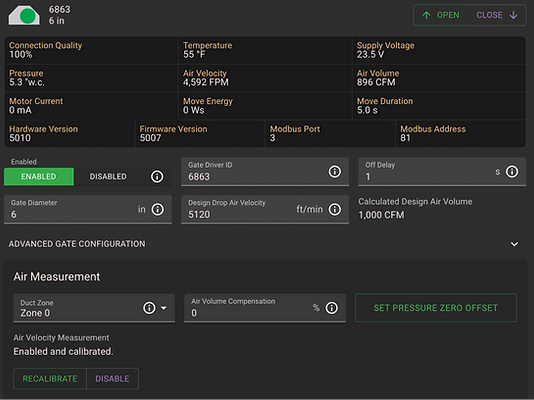
No one else provides comprehensive, system-wide monitoring for dust collection. Some competitors only do this for their own filters.
​​
It tracks air velocity and air volume at every workstation, in each branch duct, and along the main duct — as well as the operation of every dust collector subsystem, including motors for rotary airlocks, screw conveyors, transport fans, and more.

Example of industrial sensors with dry contact output:
Bin full, Airlock is Not Turning, Hopper Full etc.
Example of industrial 4-20 mA analog sensors: motor and fan vibration, hopper level, conteyner sawdust level, vacuum pump pressure, 2nd filter pressure (for example HEPA filter)
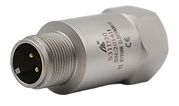
LED Status Light

Buttons to Start and Stop the dust collector


Substancial Savings

Data
Analytics
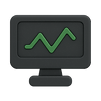
Real-Time
Monitoring

Noise
Reduction

Smart
Automation

Reduced
Maintenance

System-Wide Visibility & Control

Remote Access & Automatic Updates

Dynamic
Capacity
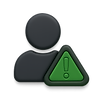
Early Issue Detection
A truly visionary upgrade to a critical factory system that directly addresses the challenges faced by overburdened factory maintenance teams. It provides full visibility into dust collection system health, delivers early warnings and fast diagnostics that help pinpoint exact fault sources, and ultimately reduces troubleshooting time. By automating an often-overlooked and energy-intensive system, it not only cuts costs and energy usage but also empowers maintenance personnel, making them more effective and valued. This innovation enhances operational safety and efficiency, transforming how dust collection systems are managed in modern industrial environments

%202.png)

Real-time airflow monitoring at every gate

Fan Power in relation to Air Volume
​
Power Consumption ∝ (Air Volume)^3
10% reduction in airflow =
~27% energy savings
25% reduction in airflow =
~68% energy savings
50% reduction in airflow =
~87.5% energy savings
Least expensive way to operate industrial ventilation systems.
​
Average return on investment (ROI) is 1-3 years.
Electricity based on usage & demand
​
-
Automatically track and report real usage
-
See which machines are routinely used
-
Average usage over 50% is rare
​
Real information allows for accuracy in decision making

Electricity Savings Calculator
ecogate.com/electricity-savings-calculator

Return on Investment Estimator
